Applications
Applications operating at or near atmospheric pressure must incorporate mechanical equipment, such as blowers and vacuum pumps, or a venturi/eductor to negate the head pressure from the system and ensure vapors from the process are collected, captured, and controlled. In applications with inconsistent flow rates where mechanical devices or venturis are deployed, there is a continual extraction of vapors from the target process, which can lead to stripping of additional contaminants, increasing chemical spend.
Challenges
- High variability of contaminant concentrations
- High variability in vapor stream flowrate
Challenges for Other Control Devices:
- Designed for specific concentration range and flowrate
- Conditions outside of design lead to:
- Inefficient carbon usage (premature carbon spend)
- Potential safety concern: heat of sorption
Case Study
A Gulf Coast Refinery was experiencing issues with elevated benzene levels shown on fenceline monitors. The source was found to be emissions coming from internal floating roof tanks with leaking seals on the internal roof. The client reached out to Vapor Point regarding possible solutions. Vapor Point’s proposed solution included utilizing the our On Demand Vapor Control System with two VaporLock™ VOC Scrubbers containing VaporSorb followed by two carbon cans to act as a polisher.
The client added a PRV to the external roof on the tank to allow for the On Demand Vapor Control System to be able to operate. A redundant flow manifold linking the three 48” VaporLock™ VOC Scrubbers in combination allowed for two scrubbers to be in operation in a lead/lag orientation with a third on standby for when the lead vessel became spent. This allowed for continuous operation, as the lag vessel moved into lead service while the standby vessel became the lag and the spent lead vessel had the chemical changed out.
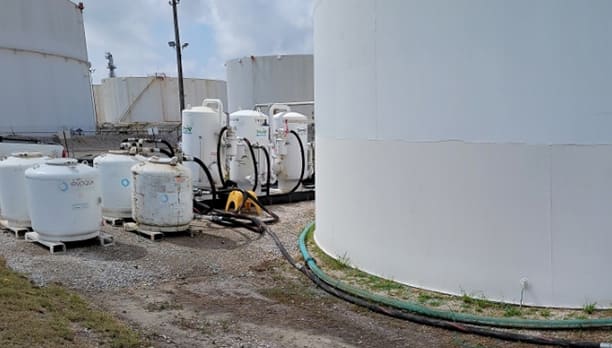
Solution
Vapor Point developed On Demand Vapor Control, a pressure sensitive automated system that allows us to modify our standard vacuum venturi controls by eliminating the continuous extraction of vapors. Our recovery system responds to pressure changes in the upstream process to open or close the venturi air supply valve, which engages or disengages the Vapor Point vapor recovery system. On Demand Vapor Control allows for a set point activation of the vacuum venturi and control system at pressures just below the operating pressure of the process/tank pressure relief device. Set to inches of water, the system senses when pressures within the tank begins to rise. When this occurs, the air supply to the venturi is opened, allowing for the excess vapors to be relieved from the tank through the scrubber system. When the pressure decreases below the setpoint, the air supply to the venturi is turned off, shutting off the system.
Due to the sensitivity of the On Demand Vapor Control Sysem, our recovery systems can be used on process streams with pressures as low at 2 inches of H₂0, or 0.07 psi. The On Demand Vapor Control System is utilized in conjunction with Vapor Point’s VaporLock™ scrubbers to capture a variety of contaminants, including, but not limited to, H₂S, ammonia, benzene, and other VOCs.
Advantages
- Optimizes chemical efficiency
- Minimizes manpower for managing the system
- Reduces operating time
- Eliminates continuous extraction of vapors
- Accommodates pressure swings
- Significantly improves vapor recovery performance
- Reduced client costs (scrubbing solvent/media in the scrubbers, labor costs associated with chemical changes outs)
Results
Vapor Point’s system was installed to reduce or eliminate state and federal fenceline deviations for a Gulf Coast Refinery’s tanks. Over the course of two years - since its installation - the client has not experienced any additional fenceline deviations associated with these tanks. Vapor Point’s On Demand Vapor Control System continues to keep our client safe and within compliance - reducing potential fees, incidents, and headaches so they can focus on their daily operations.